Pullman, WA
Pullman Regional Hospital
Scope/Solutions
Shortly after construction, the hospital reported rutting and liquid emanating from joints in sheet vinyl flooring, wet and soft adhesive under carpet tile and sheet vinyl, and cracking and bulging of vinyl composition tile (VCT) installed over a moisture mitigation coating. Following replacement of some sheet vinyl flooring with an alternate moisture mitigation coating, the hospital reported liquid-filled blisters in the repaired floor finishes. SGH investigated the cause(s) of the reported flooring failures.
SGH visited the site to document distress and conduct field testing to measure moisture vapor emission rate (MVER), relative humidity (RH), and pH of the concrete slabs. We evaluated construction-phase concrete moisture test reports prepared by others, inspected the soil blotter layer and vapor retarder, and analyzed moisture mitigation product development records. We also collected samples and performed the following testing in our laboratory:
- Chemical analyses on samples of adhesive, mitigation coating, concrete, and liquid collected during our visits to the site
- Moisture content analysis on samples of soil and gravel from the site
- Microscopic examinations on near-surface sections of concrete
SGH concluded the floor finishes degraded because they were exposed to moisture contained in the concrete slab. We found the moisture mitigation coating had inadequate permeance and degraded in a high-moisture and pH environment. We recommended removing the failed floor finishes and replacing them with an epoxy-based moisture mitigation coating, leveling underlayment, and new floor coverings.
During a subsequent trial concerning the flooring failures, SGH presented expert testimony on behalf of the general contractor, helping them recover costs for repairs from the moisture mitigation coating manufacturer.
Project Summary
Key team members
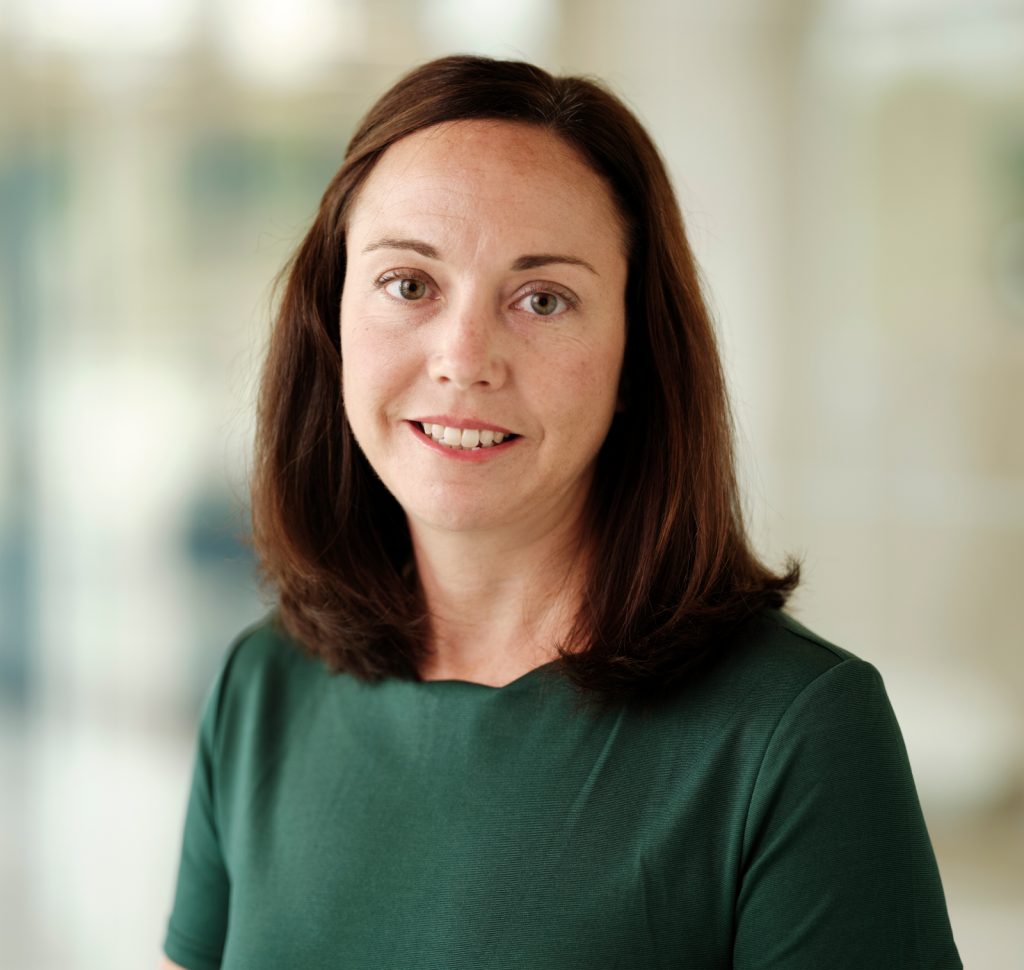
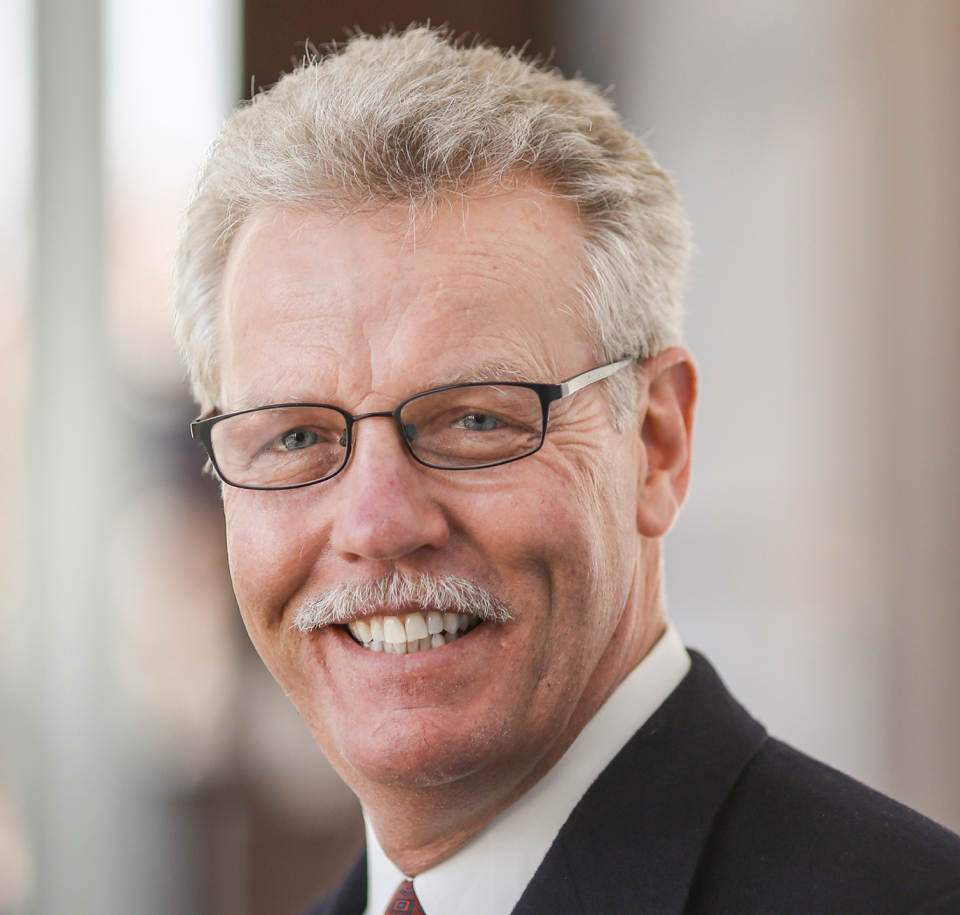