Understanding Unitized Facade Systems and Mega Panel Applications
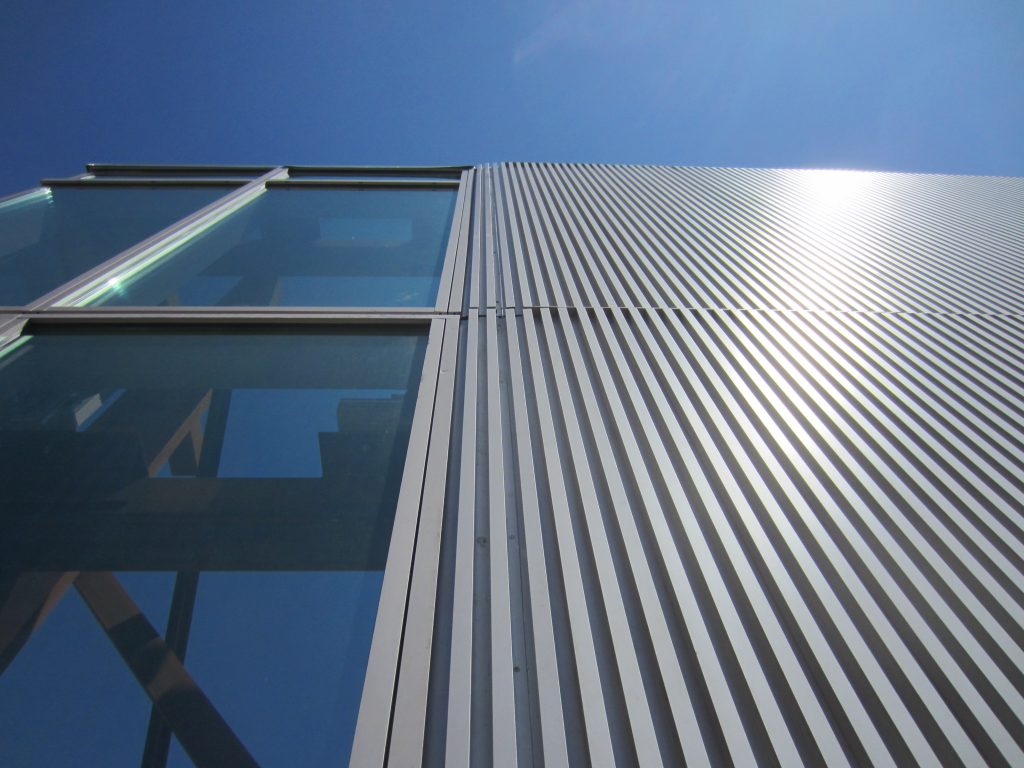
Prefabricated building enclosure systems can help project teams streamline construction schedules, reduce construction costs, and improve assembly quality. The current market for prefabricated wall systems is diverse and extensive, ranging from precast concrete wall panels and unitized glass, which are common in the industry, to mega panel walls, which are a more recent development. These mega panels allow more design options for material selection over the typical precast concrete system approach. As these systems become more popular in the construction industry, it is important to understand their benefits and limitations to achieve project success.
Prefabricating panelized enclosure systems allow for a heightened level of manufacturing precision, quality assurance, and quality control.
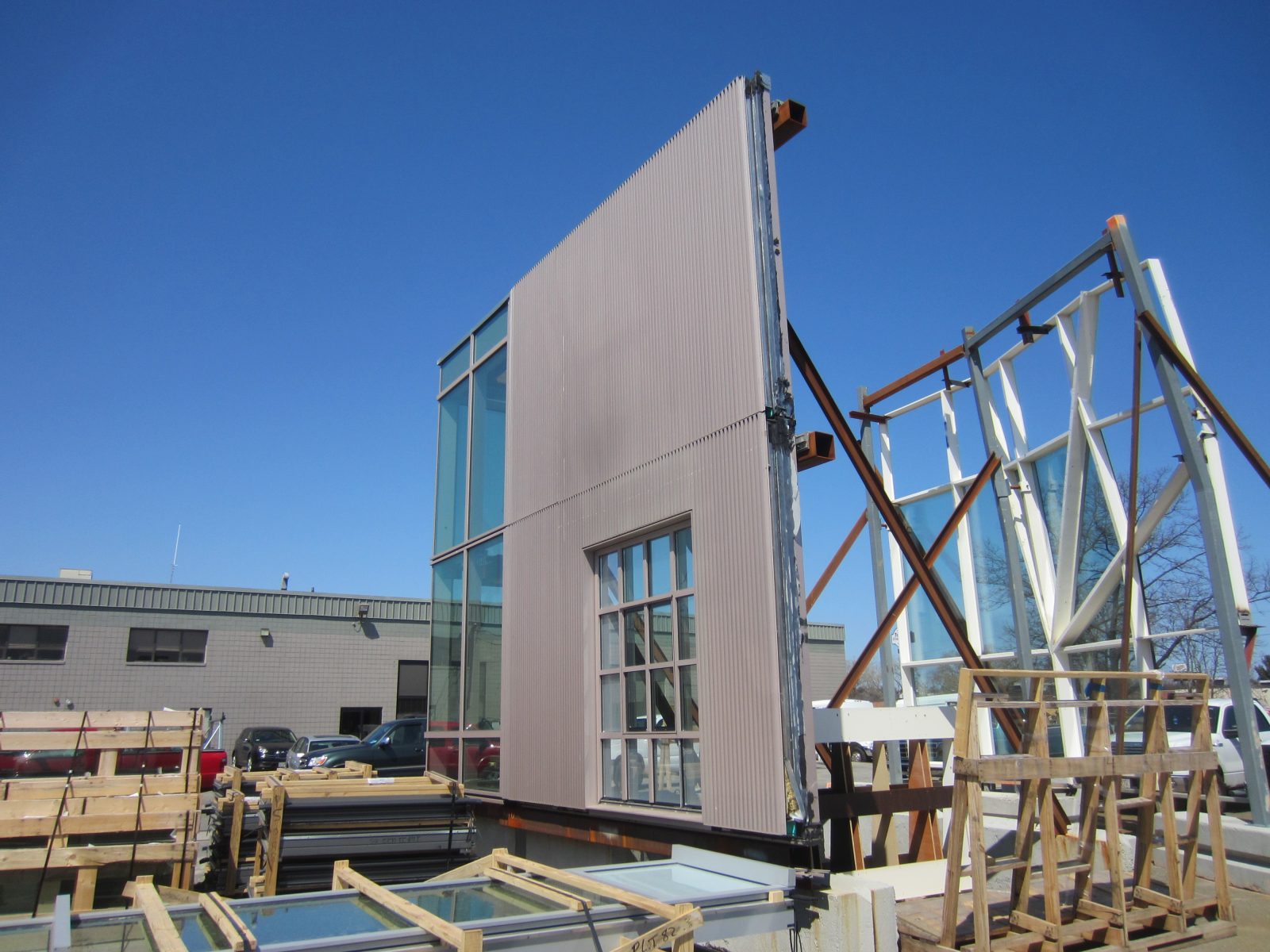
Unitized System Considerations
Project teams should consider overall objectives and fit when considering whether a prefabricated panelized facade approach is appropriate. Buildings with large exterior surface areas, simple geometry, repetition, and tight construction sites (e.g., urban areas) are all excellent candidates. Structures with less repetition, unique wall conditions or geometries, smaller surface areas, or large open sites may not benefit from prefabricated panelized systems and may be more suitable for field-fabricated (i.e., stick-built) methods.
As with standard wall systems, designers often first consider performance criteria, such as wind loads, wind-driven rain resistance, and thermal performance. In each case, there are fabrication limits and installation constraints that can affect allowable system types.
Facade choices impact many different aspects of building performance, including:
- Architectural aesthetics
- Structural systems and building movement
- Air and water infiltration
- Thermal performance and condensation
- Occupant comfort (daylighting, solar shading, acoustics, etc.)
- Security
- Fire and life safety
- Constructability
- Cost
- Durability
Mega Panel Project Considerations
A more recent development in the AEC industry are mega panels—large, shop-fabricated sections of facade that incorporate several building elements and material types. Project teams need to consider the following when designing and constructing building enclosures from mega panel systems:
- Project Fit: The ideal project is typically a larger tower-type building located in an urban environment with limited site access. The facade should consist of repetitive geometry that can be bisected easily into panels.
- Cost & Schedule: Mega panels have greater up-front engineering costs, but are typically considered cost-effective as they reduce the overall construction schedule and allow the building to become weathertight for interior finishes in weeks vs. months. Inclement weather conditions and exterior access are minimized, limiting overall project risk.
- Project Team: The project team needs to be familiar with the design-assist process and mega panel construction. The general contractor, architect, structural engineer, enclosure consultant, and panel fabricator must align and work together to be successful.
- Planning: Once chosen, the project team must design the facade around these prefabricated mega panels, including a well-defined early design package for design-assist bidding. A clear process and understanding of required deliverables are critical, as early decisions are needed on material selection and major design features that may drive up cost.
- Design-Assist & Specialty Contractors: Projects need a design-assist contractor with the ability and experience to provide full engineering, thermal analysis, and coordination.
- Architectural Layout & Aesthetics: There are many layout options based on each specific cladding system. The architect and panel manufacturer or contractor need to coordinate to lay out the panels so they are acceptable aesthetically while still optimizing materials.
- Cladding Selection: Thin brick, terra cotta, metal panel, composite panel, fiber cement, stone veneer, and other lightweight cladding materials are possible options for mega panels.
- Thermal Performance: Because joints and transitions are the thermal weak points, thermal analyses are required on a project-by-project basis to confirm that condensation will not occur.
- Joint Design: Every manufacturer’s joinery is different, and careful vetting during the bidding phase is required to understand the specific system and its performance.
- Trade Coordination & Perimeter Conditions: Think, plan, and design the mega panels carefully, considering structural connections, base building movement, windows, balconies, canopies, and any other components requiring coordination. A fully detailed set of shop drawings showing all penetrations, removed cladding areas, and transitions to adjacent systems from other trades is critical for the panels’ success.
- Quality & Factory QA/QC: Mega panels provide the opportunity to build higher-quality enclosures. The mega panels are typically fabricated on stationary work benches during flexible fabrication times within an enclosed structure, reducing inclement weather restrictions. Factory inspections and a formally documented QA/QC are critical.
- Transportation: Transportation costs are a substantial portion of the overall cost of the mega panel system. The more complex the panel geometry, the higher the transportation costs they typically require.
- Testing: Recommend performance lab mockups prior to approval and release of the system for fabrication, especially on complex projects. Field testing is critical to confirm that the provided panels meet the project’s performance requirements. Provide a full project testing plan as part of the bid package.
Important Takeaways
Prefabricating panelized enclosure systems allow for a heightened level of manufacturing precision, quality assurance, and quality control. What has historically been limited to precast concrete and unitized glass systems is expanding to mega panel wall systems and even into complete building modules. As the amount of prefabrication increases, however, project teams need to recognize the importance of early buy-in from all team members. Well-planned prefabricated panelized facade systems can help save construction time and cost, but poorly planned systems may lead to delays, added costs, and subpar performance.