Design Of FRP Shroud Structure For Mixer/Ejector Wind Turbine
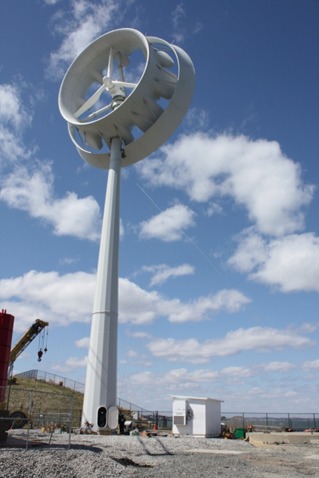
A Mixer/Ejector accelerates the air flow through the rotating blades area of the wind turbine and results in a significant increase in the wind energy that can be captured. This paper presents the design and construction of a fiber-reinforced polymeric (FRP) mixer/ejector structure for a prototype wind turbine demonstrator. The mixer/ejector design consists of two interconnected ring structures: a 12 m diameter mixer and a 16 m diameter ejector. Each ring structure has an FRP skin that works integrally with its internal light steel frame. The FRP skin has complex doubly curved lobes. The mixer/ejector is connected by a tripod to the top of the wind turbine tower at a central steel platform that also supports the nacelle and is connected to the top of the tower by yaw bearing and drive system. The nacelle contains the generator, the brakes, the controls, and the rotor consisting of a hub and the blades.
This paper presents a description of the structure, the design criteria of the FRP skin, the loads and load combinations based on the current US and international standards, the finite-element model (FEM) used for analysis of stresses and stability of the skin, the riveted connections of FRP skins and of FRP skin to the steel frame, including laboratory testing performed on riveted connections. The Mixer/Ejector is analyzed for its post-buckling strength when subjected to the design wind load. Using FEM of the Mixer/Ejector with geometric nonlinearity, the strains in the buckled state of the FRP skin are computed and compared to the allowable strains. Fatigue analysis is performed using random vibration analysis for turbulent wind and steady state dynamic analysis of rotating equipment. The paper also includes a discussion of lessons learned.
Publisher
Composites and Advanced Materials Expo