Understanding Concrete Slab Types for Waterproofing and Repair Projects
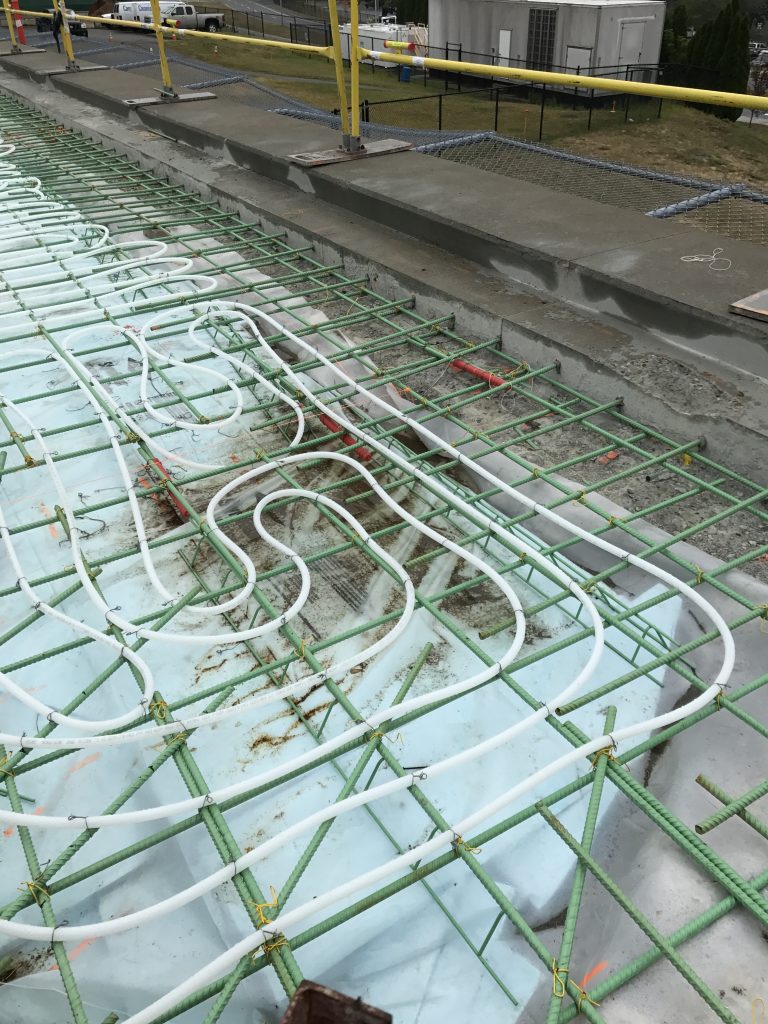
Concrete slabs are the most visible part of many waterproofing projects, especially where they support traffic and other heavy loads. In these cases, the slab is required to support significant loads—including freight delivery, parking, or industrial machinery—while also protecting the critical underlying waterproofing barriers.
Slab design and preparation is critical to a project’s success and requires close attention to both structural and waterproofing concerns during the design process. It is important to understand how different types of concrete slabs are applied to help project teams design and construct the right type of slab for long-term performance.
Slab Types
There are several types of slabs used in waterproofing, repair, and reconstruction applications, including the following:
- Mud slabs, which provide a solid and stable working surface for installing waterproofing
- Protection slabs, which prevent damage to newly installed waterproofing during subsequent construction operations
- Topping slabs, which provide additional slope for drainage prior to installing new waterproofing
- Paving slabs, which carry applied loads (due to traffic, paver systems, etc.) over waterproofing, drainage board, and insulation
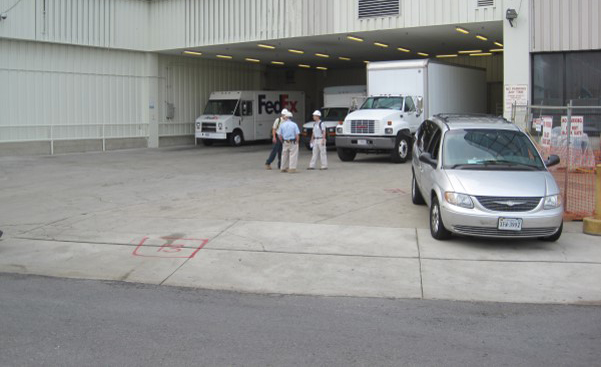
Even without a large amount of published information, project teams can successfully design and construct paving slabs over waterproofing systems by taking a multidisciplinary approach to address structural and building technology concerns.
Design Considerations

Stiffness testing of combined concrete, insulation, drainage board, and waterproofing system
Of all these slab types, the design of paving slabs is least understood because it combines aspects of conventional slab-on-grade design with the particular characteristics of the waterproofing and insulation system. There is very little published information regarding the required design parameters of this approach—most notably the effective stiffness, or “K” value, of the waterproofing and insulation system—to support the structural design of the paving slab.
While we know the properties of the individual system components to varying degrees, very little is known about their combined performance. However, SGH’s recent series of testing of these assemblies has provided new insight.
Design Process
The design process for paving slabs requires a multi-step, iterative process:
Design the waterproofing system, including addressing where joints will be installed in the paving slab and how those joints will be detailed
- Select the appropriate structural insulation to provide the required stiffness
- Develop the paving system, including coordination of the slab jointing with the waterproofing and architectural requirements
- Conduct a structural analysis and design the paving slab using the properties of the underlying waterproofing, drain board, and insulation
- Calculate the insulation deflections and associated stresses and check against the manufacturer’s guidelines
The process then continues iteratively until it meets all necessary criteria.
Ongoing Research and Discussion
We continue to learn more about how these systems perform through SGH’s ongoing research, experiences in the field, and conversations with materials suppliers and structural and waterproofing experts. Even without a large amount of published information, project teams can successfully design and construct paving slabs over waterproofing systems by taking a multidisciplinary approach to address structural and building technology concerns.