Machine Foundation Deterioration: Overcoming Typical Problems and Analyzing Root Causes
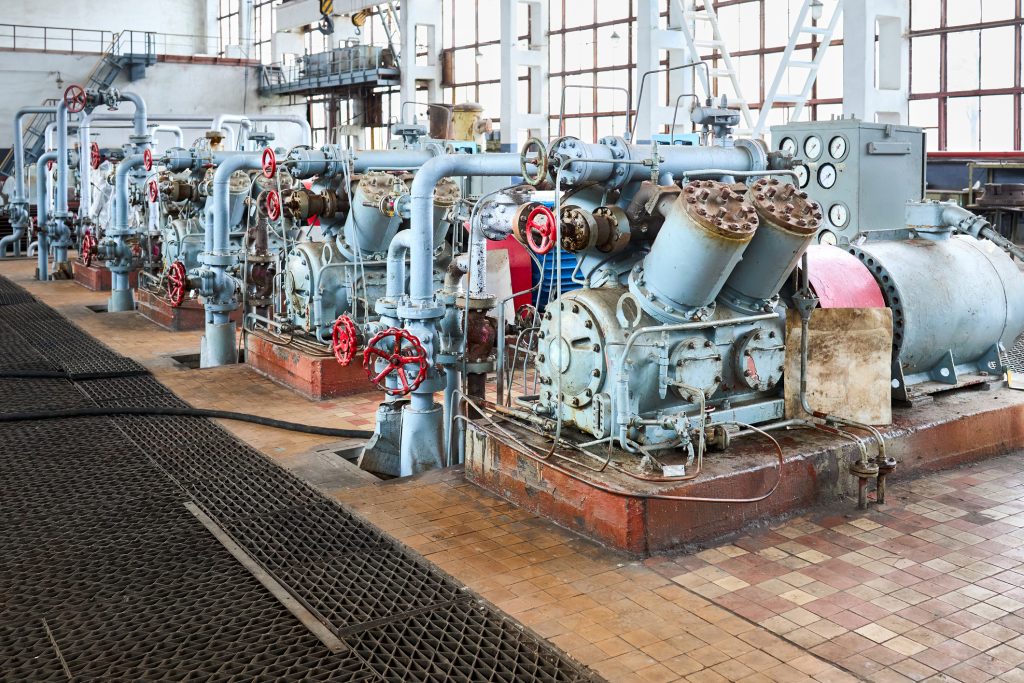
Most oil and gas, chemical, refinery, and power generation facilities have rotating or reciprocating machinery, such as pumps, compressors, and generators. The performance, safety, and stability of these machines depend primarily on the structural integrity of their supporting foundations, making foundation system design critical for the facility’s success and viability.
For older machine foundations, it was common to ignore the dynamic nature of the equipment loading along with other design factors, such as high temperatures. This was especially true at plants built more than fifty years ago due to limited available data on the performance of machine foundations at the time these foundations were built. The ensuing performance problems of these foundations may be further exacerbated in mission-critical equipment that lacks opportunities for preventive maintenance due to their continuous operation, exposure to harsh chemicals, fatigue, and thermal cycles caused by elevated machine temperatures. Since such facilities must continuously operate, wholesale replacement of their machine foundations with ones designed up to current codes may not be practical. In these situations, extending the service life of the foundations requires understanding the bases that led to today’s improved standards and finding ways to achieve acceptable performance on the existing foundations with as little intrusion as reasonably achievable.
Reliability engineers, facility owners, and maintenance authorities benefit from partnering with machine foundation subject matter experts who can implement customized, physics-based, root-cause evaluation approaches to identify causes of foundation deterioration and undertake necessary actions to maintain these critical assets and improve their performance.
SYSTEMATIC APPROACH FOR MACHINE FOUNDATION TROUBLESHOOTING
Because of the complex behavior of machine foundations, experts need to follow a structured investigation approach to ensure that the solution balances benefits with constraints. Such evaluation includes a combination of several critical steps:
-
A compressor foundation with a significant structural crack.
Define the problem scope: The first step is to discuss the issue with the owner or operator to understand the symptoms being experienced, the impact on operations, and any historical data or observations that can be provided. Understanding the history of modifications and repairs made to the foundation helps determine whether the issue could be caused by any changes to the foundation and equipment that were not intended in the original design.
- Gather existing information: It is essential to collect all relevant data, including machine specifications, foundation design documents, maintenance records, vibration data, environmental conditions, and any previous assessments or reports. It is not uncommon, especially for vintage machine foundations, that some data is not readily available. In such cases, depending on the nature and importance of the missing data, it may need to be produced through non-destructive testing (NDT), vibration measurements, or geotechnical investigations. In some cases, the missing data may also be approximated from similar plants for which the corresponding data is available.
- Visual inspection: The visual inspection intends to look for signs of distress, such as cracks, settlement, unevenness, or deterioration in concrete. A map of visible cracks should be developed during the inspection to identify the cracks’ pattern, locations, and widths. Some anchors may be visually inspected for signs of looseness or breaks. An acoustic survey can also identify potential debonding of the grout or delamination in concrete. Because the performance of anchorage, crack depths, and subsurface concrete conditions cannot be evaluated by visual inspection, other tests—such as NDT and vibration measurements—may be required to supplement the visual inspections.
- Non-destructive testing: NDT methods are often required to evaluate the performance of concrete elements when the defects are not visually accessible. There are several common NDT methods available, including ground penetrating radar (GPR) testing to confirm reinforcing layout, ultrasonic pulse velocity (UPV) testing to measure crack depths[1], and impact echo testing to identify internal flaws like cracks or deep delamination. Several other NDT methods are also available for detecting rebar corrosion, chloride infiltration, thermal mapping, and concrete cover measurements. Most NDT techniques must be performed while the machine equipment is shut down so that the excessive vibrations caused by the equipment do not mask the NDT’s reliable data. Therefore, it is essential to coordinate NDT activities with the plant operation.
- Vibration analysis: Some foundation problems can be determined by measuring the extent and severity of vibrations in the machine foundation. The issues typically detected through vibration measurements include soft feet, loose anchorage connections, broken anchorage, and resonance. Advanced knowledge of structural dynamics and signal processing techniques is required for data processing and a reliable diagnosis based on the vibration analysis results.
- Geotechnical investigation: The soil conditions underneath the machinery can significantly affect the vibration characteristics of rotating equipment foundations. The geotechnical investigation aims to understand the in situ conditions and check the presence of defects, such as pockets of weak soils. This information will inform the engineer about changes concerning the as-designed condition due to aging and improve the accuracy of subsequent analytical investigations. The method of investigation depends on the type of data needed and specific site conditions, such as site congestion, access, data accuracy, and the reliability and certainty needed compared to cost. The most common findings from geotechnical investigations include detecting defects, uneven settlements, and voids. Geotechnical investigations also provide engineering soil parameters required for subsequent analytical investigations, including the soil bearing capacity, soil type, density, damping, and shear wave velocity.
- Behavioral analysis: It may be necessary to use engineering analysis tools such as finite element (FE) methods to model the behavior of the foundation and identify potential overstressed components and resonance frequencies considering the soil-foundation interaction. This analysis may also include non-vibratory environmental effects such as high thermal loading, which is common in specific rotating equipment types like reciprocating compressors. Estimating soil impedance needs to account for uncertainty using various soil properties. Advanced FE analysis tools can perform soil-foundation-machine interaction and stress analysis due to other unique loading conditions, such as thermal gradients. More simplified hand calculations may be used in specific applications instead of advanced analysis. Selecting the analysis method depends on the complexity of the machine-foundation system, the particular outputs sought, and the limitations of the analysis methods being considered.
- Root-cause evaluation: This stage involves analyzing the measured and analyzed data to identify potential root causes of the foundation issues. This may include inadequate design, improper construction techniques, soil properties, dynamic loads, or external environmental factors. Machine foundation experts need to prioritize the root causes based on their significance and impact on the foundation’s performance and discuss them with the project team, as some causes may be more critical than others and require immediate attention, whereas some other issues may be lived with for a little longer.
- Mitigation strategies: In this stage, the consultant and owner should collaborate to develop mitigation strategies to address the root causes identified. This may involve structural modifications, soil stabilization, or changes to operational procedures. If resonance is identified as the root cause, adding spring isolators under the machine or attaching additional mass to the foundation may resolve the issue as they can shift frequency response to avoid resonance.
- Cost-benefit analysis: The final stage of the evaluation involves assessing the cost-effectiveness of proposed mitigation solutions and considering factors such as implementation time, maintenance requirements, and long-term performance to ensure optimal outcomes for the owner. The cost benefits of temporary or long-term repair solutions should also be examined in this stage.
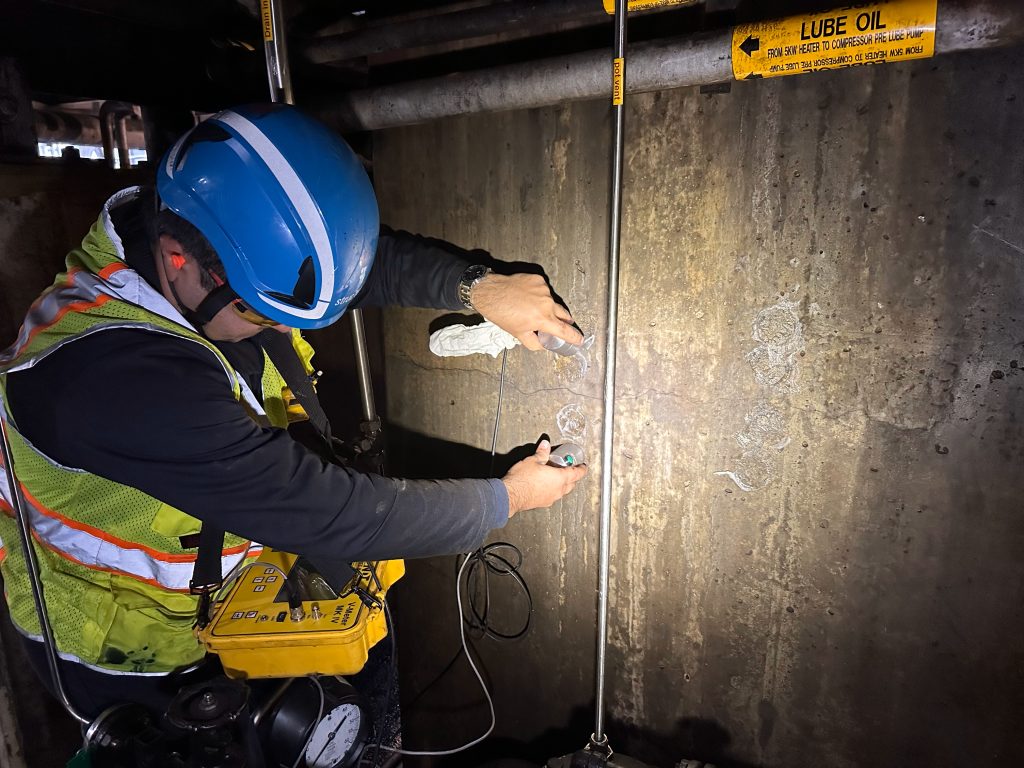
Performing UPV test on a machinery foundation to evaluate the crack depths.
COMMON CAUSES OF MACHINE FOUNDATION DETERIORATION
Understanding the common causes of machine foundation deterioration is important to help identify trends and potentially avoid downtime issues in mission-critical facilities. Facility owners and operators may come across several conditions, including:
- Soft foot: Soft foot occurs when rotating machinery is set on its base, frame, or sole plate so that one or more of the “feet” are not in contact with the supports on the frame. The leading causes of soft foot include improper contact between a machine casing and the baseplate used to support it; deformed baseplates; deformed or damaged machine feet; insufficient shims; and dirt, trash, or other unwanted materials under machine feet. Another less common cause of soft foot is excessive tension on machine feet due to anchor bolts warping the machine feet.
- Machine imbalance: Machine imbalance occurs when the mass distribution in the rotating parts of the machine (such as shafts, impellers, or rotors) is not uniform, resulting in uneven forces during rotation. Many factors can cause the machine imbalance, including damaged or broken vanes in turbines and fans.
- Misalignment: Misalignment is the most significant and damaging consequence of soft foot. However, it can also be caused by other factors, such as foundation settlements and machine imbalance. Misalignment can have adverse effects on both the rotating machine and the foundation. The most noticeable impact is vibration, which can damage the machine’s bearings, shafts, seals, couplings, and other components.
- Resonance: Resonance occurs when the foundation-soil system’s natural frequencies are near the machine’s operating frequency, causing severe vibration. The natural frequencies of the foundation-soil system may change as the foundation ages, causing resonance issues that did not exist in the past.
- Loose anchorage: The anchor bolts may lose their tension, especially in older foundations, due to inadequate unbonded length; use of L or J bolts, which may straighten out over time; fatigue; loss of bond due to concrete microcracking; inadequate development length; and inelastic deformations caused by overtightening or vibration-induced stress. While periodic retightening of connection bolts to the original preload level can temporarily alleviate the issue, it may not necessarily resolve the root cause of loosening the connections in the long term.
Accelerometer attached to a compressor shaft casing to benchmark vibration levels.
- Geotechnical issues: Geotechnical conditions—such as poor bearing capacity or lack of stiffness—can lead to foundation resonance, vibrations, or settlement. Changes in underlying soil conditions for various reasons—such as washout—can also change the dynamic response of rotating equipment. This can result in performance issues and foundation damage.
- Concrete material issues: Microcracks can form on the concrete surface for various reasons, such as plastic shrinkage caused by water loss from the surface of newly laid concrete. If oil leaking from the equipment is present on the concrete surface, surface cracking will cause further oil penetration into the concrete, resulting in concrete hydrocarbonation. Furthermore, surface cracking can create a passage for carbon dioxide (CO2) to penetrate the concrete substrate, causing carbonation. Surface cracks can also facilitate chloride penetration into the concrete, causing corrosion of the steel reinforcement. Finally, inadequate concrete compressive strength can lead to premature deterioration.
- Grout issues: Hairline cracks visible in the shoulder of the grout are common in machine foundations and can cause water ingress if the foundation is outdoors and subject to weather. Welding to base plates after grout installation can also cause thermal expansion of the base plate, resulting in spalling or cracking of the grout. Grout shrinkage can create gaps between the compressor and the grout, resulting in increased vibration levels that exceed safe operating levels.[2] Epoxy grout is generally recommended for machine foundations due to its higher resistance to chemicals, shock, and vibratory loads,[3] except when the foundation is subject to significant temperature changes. Replacing the foundation grout requires careful selection of the grout material to ensure its compatibility with the operating environment, including temperature. Additionally, the grout and substrate concrete interface should be designed to accommodate the stresses induced by the equipment’s dynamic loading.
- Inadequate structural details: A common structural detailing issue observed in vintage designs is in the anchor bolt detailing. Machine foundations designed before the 1980s do not follow today’s standards for anchor bolts, potentially causing vibration issues. Special repair techniques can be implemented to alleviate these issues.
- Inadequate maintenance: Insufficient maintenance—such as lack of inspections, lubrication, or failure to monitor vibration levels—can allow problems to go unnoticed and worsen over time.
Accelerometer attachments to a foundation anchorage and concrete surface to identify loose anchorage or soft foot.
CONCLUSION
Due to the complexity of machine foundation dynamics and unique details, reliability engineers can benefit from engaging specialized experts to complement machine foundation troubleshooting. These experts should have in-depth knowledge of the tools and methods for root cause evaluation of the machine foundation problems. They must also understand the effects of in-service degradation of the rotating equipment, foundation, and soil on the machine’s performance while being familiar with nondestructive testing, vibration monitoring, and advanced structural dynamics. The insights gained from these assessments will help reliability engineers, owners, and maintenance authorities understand the root cause of the equipment deterioration, select the best mitigation strategies to enable the continued operation of their equipment, and minimize the risk of unplanned facility shutdown and future maintenance costs.
REFERENCES
- ASTM International (2023), ASTM C597-16, Standard Test Method for Pulse Velocity Through Concrete.
- American Concrete Institute (2018), ACI 351.3R-18, Report on Foundations for Dynamic Equipment.
- American Concrete Institute (2012), ACI 351.1R-12, Report on Grouting Between Foundations and Bases for Support of Equipment and Machinery.